Plastic optics : a complete guide
Speaking of optics one naturally thinks about glass components, but in recent years, optical components in polymers are more and more used without us noticing there presence. Optical plastic components are even mixed with glass components in many objectives assemblies as for example mobile phone ones.
Why using plastic optics ?
There are many reasons why an optical designer may choose plastic optics instead of glass optics :
- Plastic material is way cheaper than glass
- Plastic injection is a high repetability process, making high quantities productions very competitive, especially if a mold tooling is done with several cavities.
- Polymers are lighter than glass, by a ratio of 2 to 5
- Aspherical lenses are not more expensive to produce than spherical lenses.
- Complex shape including mechanical mounting can be included in the part design and therefore directly injected.
- Plastic optics can be coated too, with Anti-Reflect coating to enhance optical performances or high reflection coatings like aluminium, silver or gold for optical mirrors.
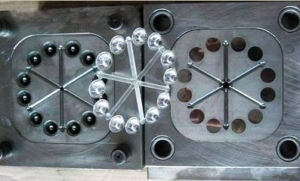
Plastic lens cluster and molding cavities
Which polymer resin to use ?
Even if the choice of polymer materials in not as wide as the choice of optical glass, especially in the range of optical index, there are different materials that can be considered. Below table show the most common thermoforming resins used for plastic optics and their main characteristics :
Polymer | Refractive index | Transmission | Operating T° | Density | Water absorption | Comments |
---|---|---|---|---|---|---|
PMMA (Acrylic) | 1.49 | 92% | 85°C | 1.18g/cm3 | 0.3 | Good transparency and mechanical stability |
PC (Lexan, Makrolon) | 1.59 | 89% | 120°C | 1.25g/cm3 | 0.2 | High resistance to impacts, more expensive than PMMA |
Polystyrenes | 1.59 | 88% | 75°C | 1.05g/cm3 | 0.1 | Cheapest optical polymer, softer material |
COP Cyclo Olefin Polymer (Zeonex, Zeonor) | 1.53 | 92% | 135°C | 1.02g/cm3 | very low | Low stress birefringence, low water absorption |
Polyester | 1.61 | 90% | 125°C | 1.22g/cm3 | 0.15 | High index and expensive material |
It is to be noticed that plastic materials refractive index are reducing with the increase of temperature, therefore plastic optics optical properties are less stable than glass in case of temperature variations.
All above plastics are almost limited to transmission in the visible and NIR, some specific plastics have a better near UV transmission, but usually polymers are aging easilly with UV exposure.
Design and manufacturing constraints.
Optical components in plastic can be manufactured either by machining (CNC or Single Point diamond turning) or plastic injection. Except for prototyping most of the interest of plastic optics is coming from the injection process, we will therefore focus on it only.
Plastic injection is done by injecting melted plastic pellets at high pressure (around 100T depending of the press size) into a molding tool. The material will be clamped in the mold for a certain amount of time (several tens of seconds) and then cooled and released by opening of the tool and ejection.
Designing optical components for injection should follow some rules to take into consideration process constraints :
- Parts should include a draft angle, that will ease the unmolding of the parts. Missing to do so will lead to difficulty in unmolding and therefore deformation of the parts.
- Polymers are shrinking when cooling, therefore parts will be a little smaller than the mold cavity.
- The thicker the part the longer the time to inject it, so the more expensive it will be
- Parts with strong difference of thickness are more difficult to inject and these differences may lead to shrinkage on the part.
- Surface accuracy near the part edge is not easy to control
Where to buy plastic optics ?
Molding of plastic parts for optical purpose need experience in order to achieve optical specifications. Key points are the ability to design and produce high polishing cavities, ability to have extra clean injection routes (no non optical polymers in it), and good control of injection pressure and clamping time.
Therefore it is recommended to work with specialists optical plastic injectors, they also often are able to produce samples from single point diamond turning to validate a design.
Don’t hesitate to contact SINOPTIX for more information or a request for quotation.