Glass working : mechanical polishing, fire polishing, which difference?
Glass, whether it is float glass, borosilicate glass or quartz glass (fused silica) is widely used for technical components. It is appreciated for its high mechanical resistance, its withstanding of chemicals, and bearing of high temperatures (borosilicate, fused silica).
While glass is almost always translucent, it is not always transparent, it depends of it’s surface quality. In order to have a good vision through a glass part it is necessary that the two external surfaces have a low roughness (material grain not visible on the surface) and a very good flatness (no waves on the material).
Mechanical polishing
For common optical components (lenses, prismes), polishing of the parts is done by friction of a polishing tool on the surface of the material. This process that gives a good optical transparency is also usable on other parts like glass tubes, glass rings and other machined glass parts.
On the other side, this process takes a long time to be done and as it needs the contact of the polishing tool to the surface of the material, is limited in the shape of the parts it can polish.
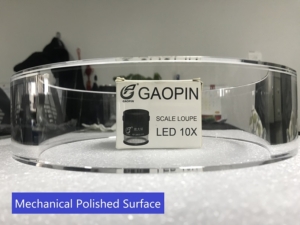
Mechanical polishing on a quartz ring
Above picture shows the good optical quality of a mechanically polished quartz ring. The image of the product inside it is very clear.
Fire polishing
Also called flamme polishing, as it correspond to a heating of the surface of a glass part with a torch. It will result in local softening of the glass that will reform with a smoother and more homogeneous surface.
This process is mainly used to polish glass tubes edges or to smooth a surface. Although it is called polishing, quality of the resulting surface is far from the optical quality of the mechanical polishing. If an object would be seen though a fire polished surface, this object image won’t be neat.
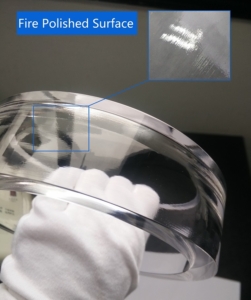
Fire polished quartz ring
As we can see on above picture, the image of the gloved fingers through fire polished quartz ring is not very neat. By zooming on the material surface (top right corner picture), striae on the material can clearly be seen.
Summarizing chart
Polishing process | ADvantageS | CONS |
---|---|---|
Mechanical polishing |
|
|
Fire polishing |
|
|
Other cases
It is interesting to note that float glass, which is commonly used for windows glass, does not require further polishing after it’s manufacturing, the good surface aspect came directly from the production line.